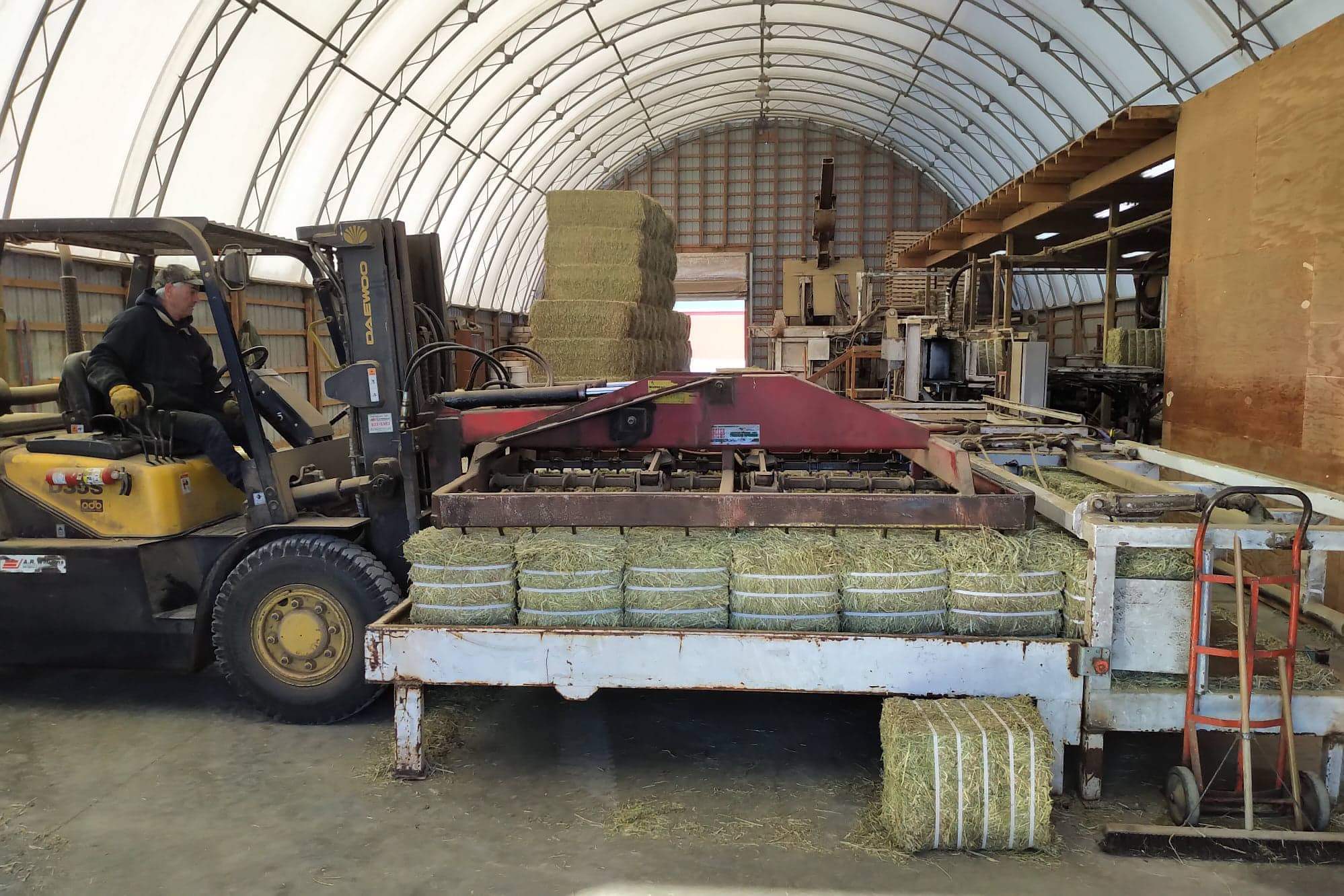
The Co-operative’s Project
For More Information and to Join …
Follow the Co-operative on Twitter.
For more information, or to obtain a Membership Application, please feel free to contact any of the Co-operative’s Directors
Thank you to our website sponsors!
Bronze Level